The pair of minimalist houses on DC’s fashionable Foxhall Road stand a bit taller and appear more modern than their more traditional neighbors. Otherwise, they resemble any other home. You’d never know they were built by robots in Baltimore.
“I don’t want to be in a space where we’re doing the same stuff as everyone else and it doesn’t improve anything,” says developer John Thompson. “The construction industry is one of the easiest to see where the flaws are.”
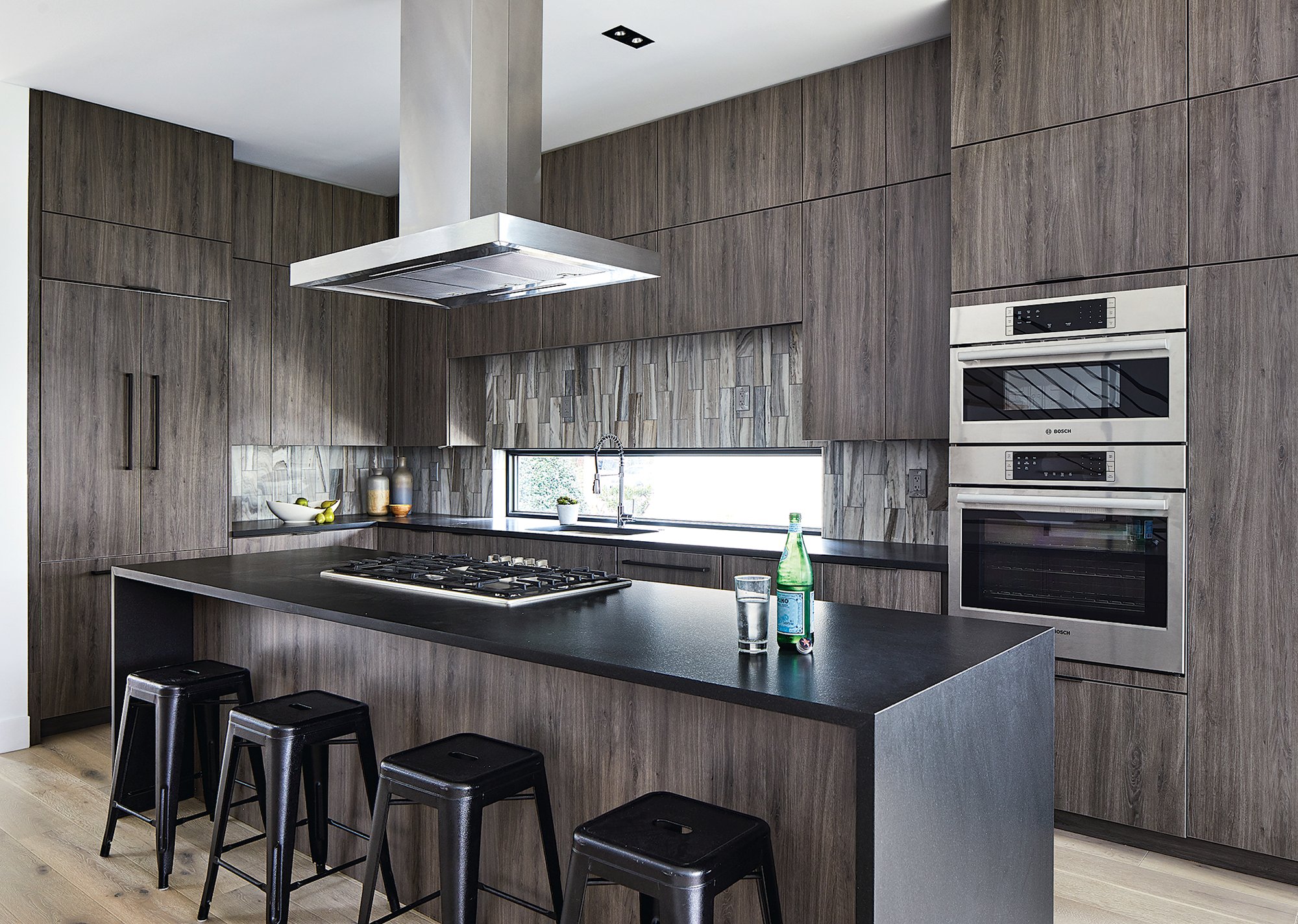
He and his partner, Steve Salis—owner of Kramerbooks and the Ted’s Bulletin chain—say they’ve resolved at least some of those flaws with their building technique. After years of researching prefabricated construction—in which components of a building are created off-site, then transported to and assembled on the lot—the pair landed on Blueprint Robotics as their supplier. The company’s Baltimore factory uses aerospace robotics to construct flat panels that are then assembled into walls, roofs, and floors.
Compared with human-dependent prefab factories, says Thompson, Blueprint’s product is unwavering in its quality: “You’re talking about putting a plan into a computer, and the robots are spitting it out consistently every single time.”
Also appealing is that building with flat panels works well for tight urban lots. Many other modular builders create large three-dimensional boxes that are put together with a crane like giant Legos. On a dense DC street with power lines and trees, hoisting and assembling such clunky components would be next to impossible.
Once the panels arrived at the lots on Foxhall Road, crews erected the houses within a week. From there, they were outfitted with finishes and appliances, just as a typical home would be. Their sophisticated interiors include whitewashed oak floors, Porcelanosa bathroom tile, and custom kitchen cabinets. Thompson and Salis say they were able to use more luxurious finishes because of the savings involved in a quicker, more predictable building process.
The houses—the first built in the District using Blueprint’s aerospace robotics—were under contract at publication time for $2.3 million each.
Though their first two projects are high-end, Thompson and Salis are looking into expanding into a range of prices. “The process is the process, whether we’re building $100,000 dwellings at an affordable level or 4,000-, 8,000-, 10,000-square-foot properties,” says Salis. “We think we can build up and down the stream.”
This article appears in the December 2018 issue of Washingtonian.